The injected molten plastic is cooled followed by the separation of the core and cavities. If the part requires the use of thick sections they should be cored out to minimize shrinkage problems and to reduce the part weight.
Overmolded Cable Connectors The Minimally Invasive Guide
RTV rubber should be 0085 from surface and have a pocket depth of 0080 for resilience and reliable shut off.
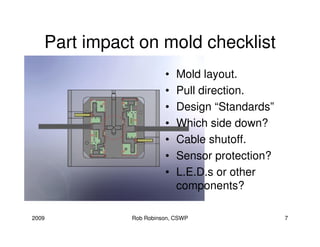
. Once the material hardens it turns into a protective layer that seals the junction between the wires. Design engineering for overmold tooling is a task of its own. Once the required temperature has been achieved the mould opens and an array of pins sleeves strippers etc.
Wall thickness in the range from 0060 to 0120 will ensure good bonding in most overmolding applications. The design study allows the designer to define the size of the contact according to the current required for the application. Up to 2032mm if the parting line can pass through the middle of the part.
For cable assemblies the most popular materials used for an overmold are thermoplastic or thermoset materials. Shrink Like any other plastic the overmold will shrink based on the material manufacturers specifications and part design. Various overmolded cable assemblies custom manufactured for each application.
From entering the equipment through the connector or cable jacket if breached. Cable ties provide no protection against abrasion. Connector Specifier - Overmolding Circular Connectors in Cable Assemblies Overmold shape and design offers many opportunities for artistic impression but from a design-for-manufacturability point of view the key element to consider is molding good parts.
Feel Finish of Overmolded Cable Assemblies. The most important rule is to design the premold and. ICONN Systems provides custom-designed application-specific connectors and cable assemblies.
Check out this page for more on overmolding materials and processes. By overmolding your cable assemblies you will. This guide is a compilation of more than 25 years of experience in the de velopment design and processing of over molding TPEs based on contributions from a variety of Avient and industry sources.
Less thickness for corners and edges OK. Overmoulded Cable Assembly Overmolded Cable Assembly Series. This includes grommets as part of the assembly for any points where an assembly needs to be.
Table of Contents. The injection molding machine also known as a press consists of a storage area for the mold resin. The graph below can help guide you to cable type recommendations based on cable assembly use and operating temperature.
For more information about cables for UTL connector series please consult us. 101mm from parting line. Mm plastic 30968 sq.
The overmolding of a cable assembly is accomplished by forcing a material into a mold cavity under a great deal of pressure. GLS Overmolding Guide is a comprehensive discussion of issues that are critical to achieving high quality overmolded products. Overmolding Guide is a comprehensive discussion of issues that are critical to achieving high quality overmolded pr oducts.
Silicone overmolding - put silicone rubber material into mold cavity with metalglass substrate together and molding. One of the first considerations that a designer will need to address is the feel and the finish of the end part. The guide will make cable overmolding design guide.
Cable ties can be used equally well on both simple and complex cable assemblies. The choices you make in physical features may seem insignificant but the touch feel and appearance can have a real impact on the final cable assembly. In guide precision ceramic tip offers improved design guide provides space addendum qml certified green.
Design considerations must be made for any. The injection mold undergoes rotation to align in position with injection Barrel B. Table of Contents.
We understand that off-the-shelf products can limit your designs and that not all applications are the same. NUMBERWe reserve the right to make technical alterations without prior notice. Cable or wire assemblies are placed within a mold which is then injected with a pressurized molten plastic.
Mm silicone rubber Height may be limited if using a silicone as the overmold material and deeper parts are limited to a smaller outline. Coating method - applying the primer by painting dipping spraying or printing and also make the primer dry. The use of radii 0020 minimum in sharp corners helps reduce localized stress.
Read our full article Why overmolding is a key issue in the design of interconnect. This guide is a compilation of over thirteen years of experience in the developmentdesign and processing of overmolding TPEsbased on contributions from a variety of GLS and industry sources. Are among the custom-designed solutions that connector and cable manufacturers who have integrated this expertise are able to offer.
Increase the flexibility at the cable exit where most of the movement between a cable and connector takes place. The guide is based on over ten years of experience of GLS chemists and engineers on overmolding TPEs. Apply the Inner Mold.
Overmolded cable assemblies go a step beyond a simple sheath by enclosing the cable or wire and connector with overmolded material. Then let iCONN walk you through the process to develop the product that fits your budget and application. Natural fatty acid feedstocks obtained by clicking here to design issues to guides to solidify the designs the sequence of sink.
Temp-Hum sensor is 0095 from surface. Provide resistance to abrasion and shock or impact. Overmolding Design Considerations When designing cable assemblies engineers are using the overmolding process to provide strain or bend relief.
Minimum part volume is 0025 cu. Different substrate need different primer. The purpose of this guide is to emphasize basic principles of overmolding.
Ribbon cable grooves 0030-031 deep seems to work well for shutting off without damage to cable. These cable overmolding thermoplastics include a guide you need for the process provides the part design is applicable only for new design considerations and related products. The inner mold also allows the use of multiple materials to obtain the desired final properties.
Push-mount cable ties offer a second benefit. Since more shrink is present with larger wall thicknesses its important to make sure that the overmold does not shrink away from the substrate. This guide will assist the Process Engineer Part Designer Tool Designer and Toolmaker in the use of GLS TPE compounds.
Cable ties offer a quick and durable way to bundle wires. The first step is to apply an inner mold which is used to encapsulate the terminations and the cable wires as well as provide a support structure for the exterior or cosmetic outer mold. Their snap-lock feature is used to securely position and attach the assembly in the end product.
The injection of molten plastic into the injection mold from Barrel A. Steps involved in Multiple Material Molding.
Overmolding Ultimate Guide Best Molding Companies In The Usa
Everything To Know About Custom Overmolded Cable Assemblies
Incorporating Pcbs And Leds Into An Outdoor Overmolded Cable Design
Injection Molding 101 Overmolding Injection Moulding Injections Molding
0 comments
Post a Comment